Reliable Power, Peak Engine Performance, Lower Emissions
Njord Filtration is an innovative 'One Stop Shop' for optimizing and keeping fuel oils and other liquids in excellent condition. In addition to delivering a wide range of products, systems and services, no one is more capable than us at analyzing and solving your problems.
Below you will find our interactive Problem Solving Diagram specifically for diesel fuel.
Problem Solver
Select your problem
Select your action
Our solution
FUEL TEST
If there are problems with filters, injectors, pumps or diesel quality in general, it is advisable to take a bottom sample from the tank(s) and have it analysed. Sometime the diesel is so filthy that the conclusion is obvious: the diesel must be cleaned.
We offer a sampling and analysis service as well as sampling sets to take your own samples. These can also be sent to us for analysis, or can be tested for microorganisms with Liqui-Cult.
REMOVING CONTAMINATION
If contamination of the diesel with water, sediment and/or microorganisms is discovered, it is important to remove the contamination from the tank(s) and to bring the fuel back into optimal condition.
To this end we offer a tank and fuel cleaning service as well as the equipment to recondition the fuel yourself. If we clean the tank and fuel, before and after samples are taken to demonstrate the effect of service provided.
PREVENTIVE MEASURES
After the contamination has been removed, it is usually best to ensure that it cannot reoccur. With modern diesel, however, the chance of this is relatively high. There are a number of preventative measures, products and systems available for this. The choice for one of these is different for each situation, client and available budget.
We offer sampling services, complete fuel maintenance contracts and installation of preventative products and systems according to the KIWA BRL-K903-08 norm.
There are a number of options for the tanks as well as the engines/burners:
IN-LINE QUALITY MEASUREMENT
If so desired, the quality of the fuel with regard to water and sediment levels can be measured in-line in order to control the quality or to adjust the filtration system.
Njord provides:
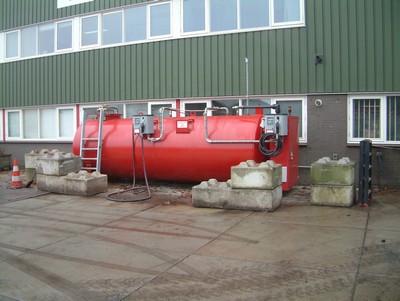
Such tanks can be equipped with a control system also managing fuel supply and tank sensors as contents measurement, vacuum leak detection systems, as well as additive dosing systems are available upon request.
- high quality fuel tank on 1% angle
- integrated automated filtration system
- water, sediment and micro-organism removed automatically
- keeps water below 50-70 ppm
- keeps fuel partivle count as required for common rail engines (better than 18-16-13)
- remote monitoring ready
- optional leak detection on return pipe and/or tank, tank contents management, additive dosing system
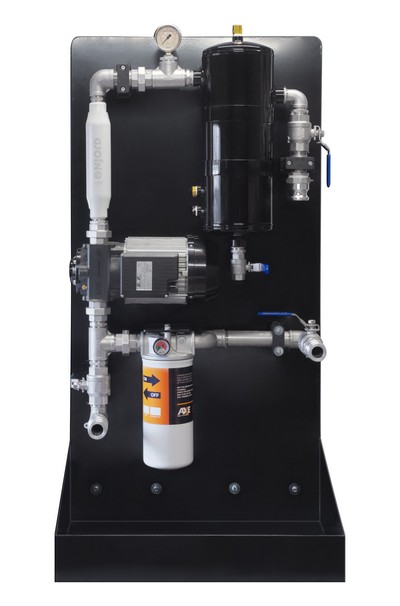
Key Features:
- Heavy Duty prefilter or coalescer to separate water and heavy sediments
- Compact design and low weight
- Absolute filtration in final filter
- Two step water separation
- Fuel Conditioner to stop micro-organism growth and stabilize fuel
- Fuel Quality required for Common Rail engines
- Including suction and return hoses
- Prefilter optional
- Filtration Controller optional
- Flow meter optional
Each fuel tank is its own biosphere. Diesel fuel is naturally unstable and forms sediments over time. As water enters the tank with the consumption of fuel, micro-organism contamination is always a threat. The drastic reduction of sulfur and addition of bio-components to diesel fuel in recent years have further reduced shelf life and increased fuel related headaches. To make sure your engines or burners run reliably and efficiently on (bio)diesel, it is strongly recommended to recirculate each fuel tank a few times per year.
To bring and keep the fuel in spec and meet the engine manufacturers’ fuel cleanliness requirements, it is essential to keep water below 70 ppm and reach at least an 18-16-13 ISO 4406:1999 particle size distribution. Multi-pass filtration with a water absorber and absolute filter elements with a high Beta ratio for filtration below 5 micron are required. This is realized using the Njord Mobile Tank Cleaning Systems running in a parallel recirculation loop to the fuel tank.
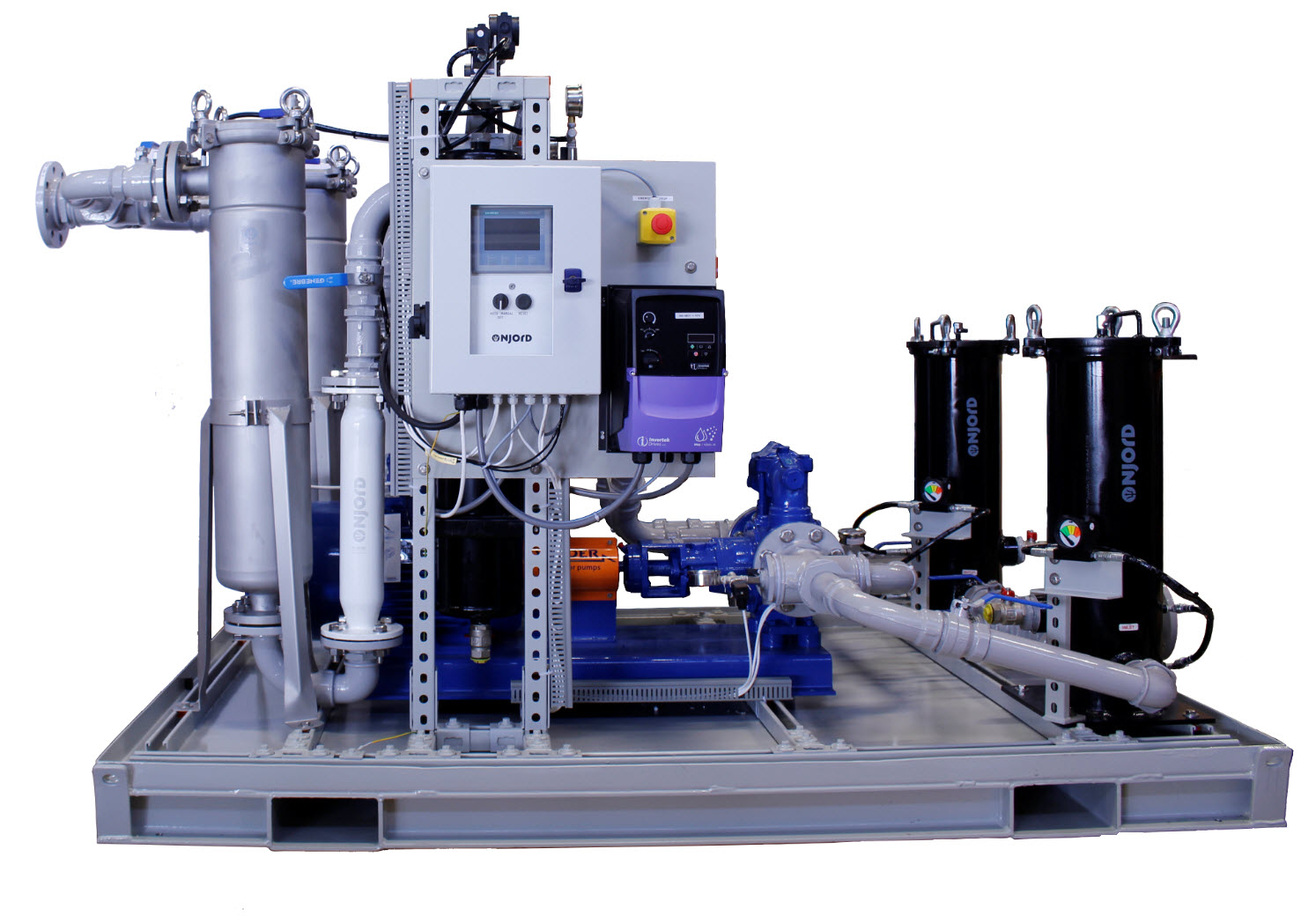
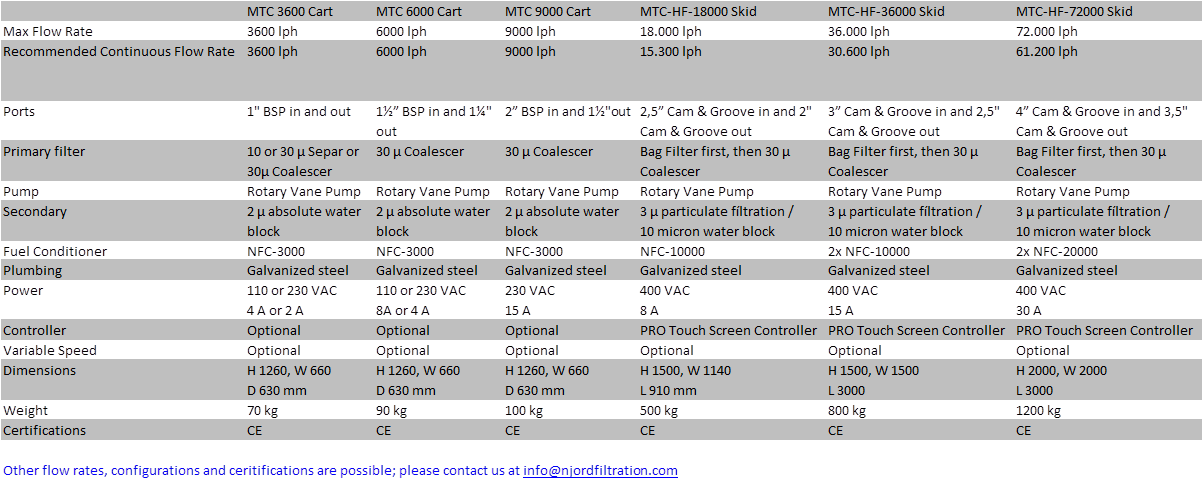
Each fuel tank is its own biosphere. Diesel fuel is naturally unstable and forms sediments over time. As water enters the tank with the consumption of fuel, micro-organism contamination is always a threat. The drastic reduction of sulfur and addition of bio-components to diesel fuel in recent years have further reduced shelf life and increased fuel related headaches. To make sure your engines or burners run reliably and efficiently on (bio)diesel, it is strongly recommended to install a fuel filtration system on each fuel tank.
To bring and keep the fuel in spec and meet the engine manufacturers’ fuel cleanliness requirements, it is essential to keep water below 70 ppm and reach at least an 18-16-13 ISO 4406:1999 particle size distribution. Multi-pass filtration with a water absorber and absolute filter elements with a high Beta ratio for filtration below 5 micron are required. This is realized using the Njord automatic Fuel Filtration Systems running in a parallel recirculation loop to the fuel tank.
Key Features:
- Automated filtration controller with week clock
- Plug & Play system
- Water, filter, flow and leak alarms
- Absolute filtration in second filter
- Two step water separation
- Fuel Conditioner to stop micro-organism growth and stabilize fuel
- Fuel Quality required for Common Rail engines
- Powder coated or stainless steel 316 cabinets
- Stainless steel plumbing
- Optional auto water drain
- Optional Multi Tank Control
- Remote monitoring ready
![]() |
![]() |
Automation can be added by the customer right away, or after some time. These systems are available in DC and AC versions, and consist of a leak tray, pump, Fuel Conditioner and single filter. The option exists to get a primary filter to aid in tank cleaning for rather dirty tanks.
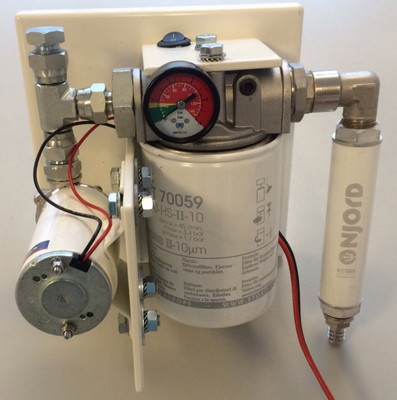
- Compact design and low weight
- Absolute filtration in final filter
- Fuel Conditioner to stop micro-organism growth and stabilize fuel
- Fuel Quality required for Common Rail engines
- Optional suction and return hoses
- Prefilter optional
- Filtration Controller and sensors optional
- Flow meter optional
Each fuel tank is its own biosphere. Diesel fuel is naturally unstable and forms sediments over time. As water enters the tank with the consumption of fuel, micro-organism contamination is always a threat. The drastic reduction of sulfur and addition of bio-components to diesel fuel in recent years have further reduced shelf life and increased fuel related headaches. To make sure your engines or burners run reliably and efficiently on (bio)diesel, it is strongly recommended to recirculate each fuel tank a few times per year.
To bring and keep the fuel in spec and meet the engine manufacturers’ fuel cleanliness requirements, it is essential to keep water below 70 ppm and reach at least an 18-16-13 ISO 4406:1999 particle size distribution. Multi-pass filtration with a water absorber and absolute filter elements with a high Beta ratio for filtration below 5 micron are required. This is realized using the Njord Mobile Tank Cleaning Systems running in a parallel recirculation loop to the fuel tank.
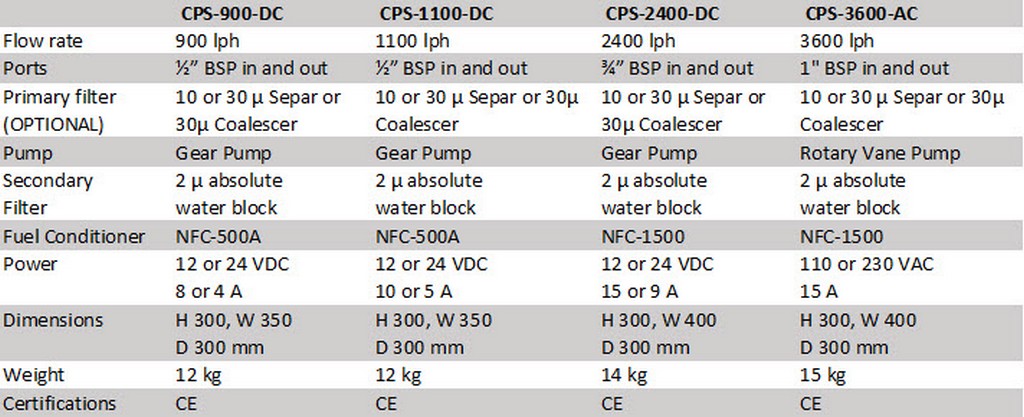
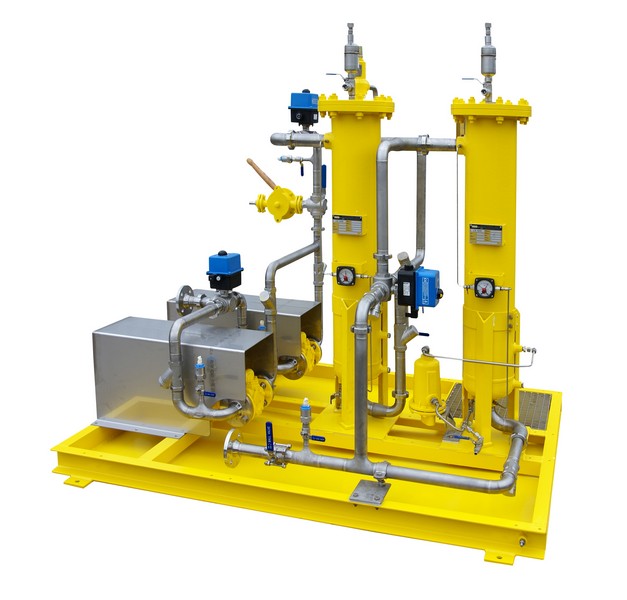
For example Fuel Forwarding Skids are used to provide gas turbines with clean fuel for start-up, emergency operation or even regular operation. Piping is generally stainless steel 316L and welded.
Fuel cleanliness requirements are part of system’s design as are environmental conditions. Commissioning services can be provided upon request.
The systems can be built to spec and can include:
- Flow rates from 25 to 19.000 lpm
- Simplex or Duplex Fuel pumps
- Simplex or Duplex Filtration / Separation
- ASME Section VIII Div. 1 filter vessels
- ASME IX or EN-287 welding specs
- 0,5 – 25 micron filtration
- Design pressure 1 – 10 bar
- Environmental temperatures -40 to +60ºC
- Vacuum, pressure, water sensors / switches
- Stainless Steel Plumbing
- Pressure Safety Valve
- Vortex Flow Meters
- In-line laser particle size and ppm water measurement
- Automated Water Drain
- Heat Tracing & Cladding
- PLC Controller
- Modbus, TCP/IP, LAN and Internet connectivity
- Remote alarm monitoring
- Dye and radiographic weld inspection
- CE, UL, NEMA, ATEX, PED, AD 2000, EN 13445, CU TR, TÜV Approval, LLOYD’S Certificate
Optional in line fuel quality measurement
Inline laser-particle counter measures particulate contamination in the fuel or oil. The sensor can also be installed independently to act as a filter system sensor or in combination with the total monitoring and management control center.
A loop powered water in oil sensor enables fast and reliable drift free inline detection and monitoring of moisture percentage or ppm water in fuel or oil.