Blogs
Fuel Maintenance Systems: Protecting Your Investment and Reducing Downtime
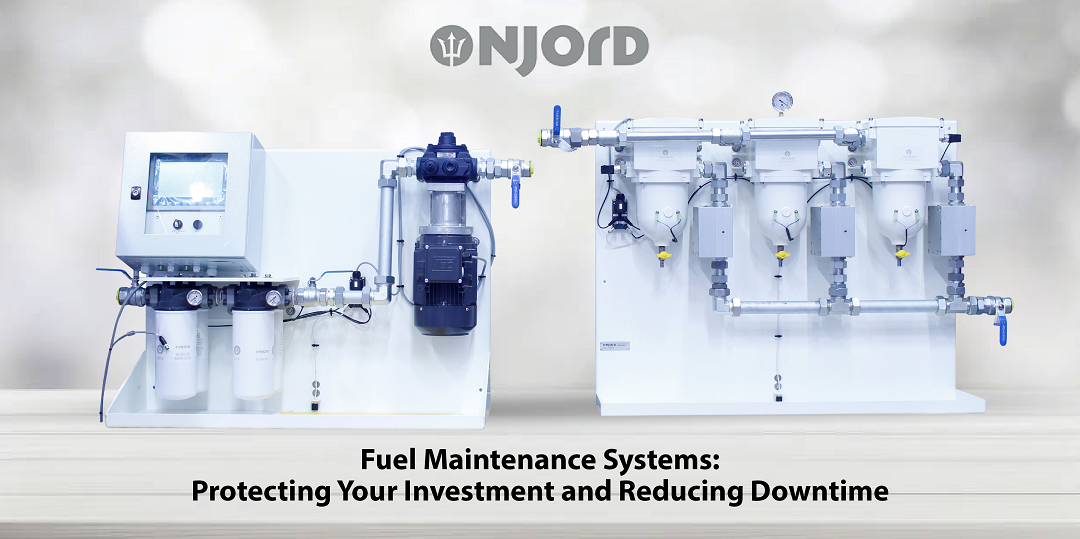
If you use machines that run on diesel fuel—like generators, trucks, or big industrial equipment—you already know maintaining uninterrupted equipment operation is essential in diesel-reliant industries. But did you know that dirty or old fuel can quietly damage your machines, even when they're just sitting still?
Fuel maintenance systems offer a proactive solution to mitigate equipment risks caused by fuel degradation. They're not something most people think about every day, but they're one of the smartest ways to protect your equipment and avoid unexpected breakdowns.
What do fuel maintenance systems do, and how do they help your business? Find out here.
Diesel Fuel degradation Over Time
The obvious thing about diesel fuel is that it doesn't stay fresh for life. When it sits in storage tanks too long, it can start to go bad. Here's what happens:
- Water gets in through air or condensation.
- Bacteria grow in the water inside the tank.
- Dirt and sludge build-up at the bottom of the tank.
- The fuel starts to break down and become less useful.
If you use this contaminated fuel in your machine, it can clog filters, damage engine parts, and even stop the engine from starting. That can impact especially during emergencies when you really need your generator to work.
Definition and Functions of a Fuel Maintenance System
A fuel maintenance system is designed to help clean the fuel and remove pollutants. It is like a cleaning and care system for your fuel tank.
These systems are usually installed on or near your fuel storage tank and work automatically. They clean the fuel regularly—even when you're not using it.
Key things a fuel maintenance system does:
- Filters out dirt and sludge
- Removes water from the tank
- Circulates fuel so it doesn't sit still too long
- Keeps fuel fresh and ready to use
It's like giving your fuel a regular checkup so it stays in good working condition when you need it.
Who Needs a Fuel Maintenance System?
If you store diesel fuel for more than a few weeks, you better rely on the fuel maintenance system.
This is a smart choice for
Hospitals and data centers with backup generators
- Construction companies with large machines
- Farms that use diesel-powered equipment
- Factories or warehouses that use fuel-powered machines
- Anyone who stores diesel for backup or regular use
Even if you only use your generator once or twice a year, keeping the fuel clean matters. A generator won't make any sense during a power outage if it won't start because of dirty fuel.
The Risk of Neglecting Fuel Maintenance
Here's what can happen if you don't take care of your fuel:
- Engines might not start
- Fuel filters get clogged
- Parts wear out faster
- Expensive repairs may be needed
- Critical systems may fail during emergencies
Most of these problems occur without warning, so waiting until something breaks is not a good plan.
Benefits of Using a Fuel Maintenance System
- Clean fuel means fewer breakdowns and less money spent on fixing equipment.
- Whether it's a generator or heavy machinery, clean fuel is more likely to make your equipment run well.
- Downtime means lost time and money. Fuel maintenance systems help prevent surprise problems that shut down your work.
- Engines that run on clean fuel last longer and perform better.
- You don't have to worry about your backup systems failing when you need them most.
Why Fuel Maintenance Make Sense?
Most people do not have time to do fuel maintenance themselves. That's why many companies choose to hire experts who handle everything for them.
With a professional fuel maintenance service you get:
- Regular fuel cleaning and inspections
- Help spotting problems before they get worse
- Fewer breakdowns and repairs
- Priority support when issues happen
It's a smart way to protect your business without adding more to your plate.
The bottom line
If you want to protect your fuel and equipment, Njord Filtration is here to help. We offer fuel maintenance systems and services to relieve your stress. Our team will keep your fuel clean and your machines ready when you need them.
Contact us to learn more about our fuel maintenance services and how we can help protect your investment.Why Fuel Polishing Essential for Mining & Construction Industries?
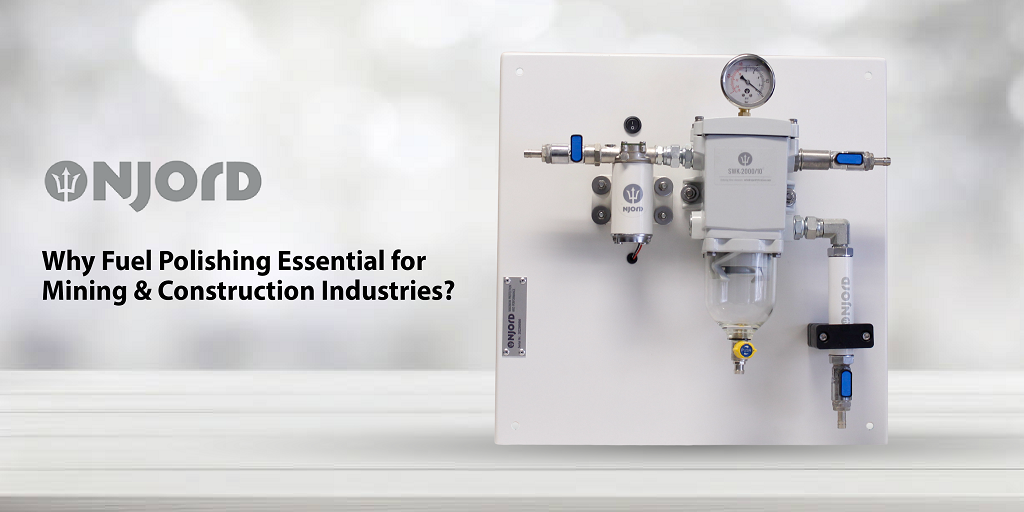
If you work in construction or mining, you know how critical your machines are. Big equipment like trucks, diggers, and generators do the heavy lifting—and they all run on diesel fuel. But here's the problem—-diesel fuel can get dirty, and dirty fuel causes big problems.
An efficient fuel polishing system is essential to ensure operational reliability and reduce costly downtime. It also keeps your fuel clean so your machines work better and don't break down. But why does that matter, and how does it help your business? Find out here.
The Consequences of Fuel Contamination
Diesel fuel doesn't stay good forever. When it sits in tanks for a while—especially outside—it can collect:
- Water
- Dirt
- Sludge
- Bacteria and fungi
These things can clog your filters, damage your engines, and even stop your machines from working. On a busy construction site or in a mine, that's the last thing you need. One broken machine can slow down the whole project. And that costs time and huge money.
The Function of a Fuel Polishing System
A fuel polishing system is a cleaning process that filters your diesel fuel. It takes the fuel from your tank, runs it through filters, removes all the bad stuff, and puts the clean fuel back.
A fuel polishing system is essential if your machine needs fresh fuel for peak operation.
The Importance of Fuel Polishing System on Construction Sites
On construction sites, fuel is stored in tanks and used to run all kinds of big equipment. Sometimes, machines sit unused for days or weeks, giving fuel time to go bad. A diesel fuel polishing system for construction industry work keeps fuel clean even when it's stored for a long time. That means your machines start-up without trouble, run better, and need fewer repairs.
It also helps reduce smoke and pollution, which is better for the environment and your team.
The Role of Fuel Polishing in Mining Operations
Mining is a bit tougher. Mines often run 24/7 and use a lot of diesel. Fuel tanks are bigger, the weather can be extreme, and the job sites are usually far from towns or help. That's why fuel system management and polishing for mining operations are a must. When your fuel is clean, your machines can keep running safely—even in tough conditions.
If you're deep in a mine or far from a service center, you don't want to deal with fuel problems. A polishing system keeps things running smoothly.
Fuel Polishing keeps everyone safer
Dirty fuel doesn't just impact machines—it can also be dangerous. Engines that fail suddenly can cause accidents. Generators that stop working during a power outage can put workers at risk.
Clean fuel means your machines work the way they should, which means fewer surprises and safer job sites. A fuel polishing system helps ensure your team can do their work without worrying about sudden equipment problems.
Recommended Frequency for Fuel Polishing
How often you polish your fuel depends on a few things:
- How long the fuel sits in the tank
- The weather (hot and wet places cause faster fuel problems)
- How clean your storage tanks are
- How important that fuel is for your daily work
Fuel should be polished at least every 3 to 6 months. If you're in a remote location or storing fuel for backup power, you might need to do it more often. The team at Njord Filtration can help you figure out the right schedule for your site.
It Saves Money (And Headaches)
Fuel polishing isn't just about keeping things clean. It can save you a lot of money and stress. Here's how:
- Fewer engine problems
- Less time fixing broken machines
- Longer life for your equipment
- Better fuel efficiency
- Less wasted fuel
Clean fuel means fewer breakdowns and more time working. That means productive workers, faster jobs, and lower costs.
The bottom line
If you want clean fuel and smooth operations, you need a good system and a team that knows what they're doing. That's where you can rely on Njord Filtration. The fuel polishing systems are tough, reliable, and easy to use. We are here to help you keep your fuel clean, your machines running, and your business moving forward.
Speak with a Njord Filtration expert today to customize a fuel polishing solution tailored to your site's needs. Let's keep your operation running cleaner, safer, and longer.”
How It Works: Offshore Fuel Tank Cleaning and Diesel Filtration System?
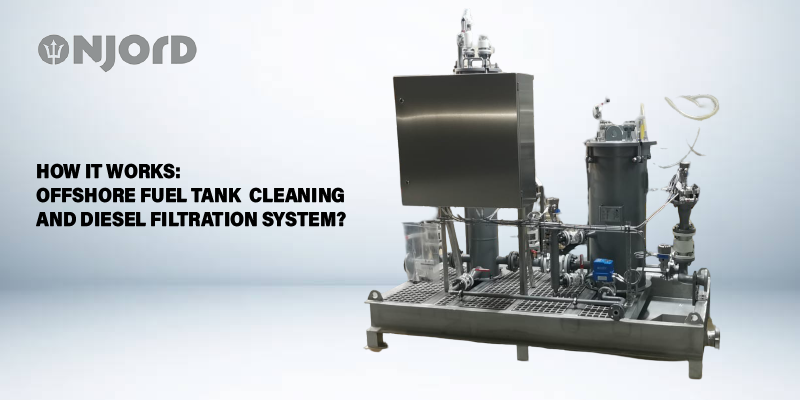
You might already be aware that the most common concern with the deployment of a diesel generator is fuel storage. For long-term and effective fuel storage, the route is pretty challenging. Well, it might feel tempting to stock it all up or leave the fuel tank empty for an extended time, but it's not without risk. This way, the risk of contamination becomes much higher the longer you keep it full or empty. At last, it can cause damage to your diesel system, and you might end up in an unfortunate situation like an unexpected breakdown in the middle of the shore. In this blog, we will discuss how you can take care of your fuel tank cleaning and diesel filtration system when offshore.
Why Do You Need Offshore Fuel System Cleaning?
When it comes to maintaining your fuel system offshore, it's one of the essential aspects which often gets overlooked. However, if you take proper care of your fuel system, then it can help to ensure optimal engine performance, increase your fuel efficiency, and improve the overall lifespan of your vehicle. Here’s a list of reasons why it is essential to get your fuel tank cleaned offshore:
Fuel Efficiency
Of course, having a clean fuel system will ensure that your fuel gets delivered to the engine the right way. It transfers the fuel in the most efficient way while minimising fuel waste, which in the end also improves your fuel economy. If you do not clean or polish your fuel tank, then fuel deposits can build up inside the injector and other components over time. This congestion will cause poor fuel atomisation and combustion, and you will see a decrease in your mileage.
Engine Performance
If deposits accumulate in your fuel tank, it can reduce your engine's power and performance. Offshore fuel system cleaning and polishing can help clear this buildup, allowing your engine to work at its optimum capacity. This way, you can get smooth acceleration and better responsiveness while onboard.
Engine Sound
When carbon deposits in your fuel tank or combustion chamber, your engine might make sounds like knocking and pinging, while running. This deposit and sound can both affect your engine's lifespan. So, with regular offshore cleaning, you can avoid the formation of this buildup. It will also ensure that your engine operates quietly and efficiently.
Fuel System Lifespan
Getting your fuel tank cleaned offshore can reduce the strain that various engine components develop over time. This can extend the lifespan of your fuel pumps, injectors, and other fuel system components. It can also reduce the risk of expensive repairs on fuel system-related issues, such as corrosion, since you can prevent it through offshore fuel maintenance.
(Also Read: How Offshore Fuel Polishing Ensures Reliable Emergency System Performance)
What are the Signs that Your Fuel Tank System and Diesel Tank Need Cleaning?
Unfortunately, a lot of owners don't realise that their fuel systems need cleaning until they notice the signs. If you are one of them or one just due for a regular offshore fuel tank cleaning, then here are some signs to tell you to schedule:
- Engine Misfiring: Your engine can start misfiring if your fuel system is dirty or clogged. This will cause your engine to make noises like sputtering and cause your vehicle to start shaking. The problem is that the injectors cannot supply enough fuel mixture due to blockage.
- Poor Mileage: The fuel injection system is designed to distribute or supply fuel in exact proportions. This proportion is necessary for your engine to have optimum performance. However, due to a buildup or a clogged system, fuel efficiency can start deteriorating due to improper supply. So, you can blame a blocked fuel injection system if your mileage gets affected.
- Performance Deterioration: If your engine is not receiving enough fuel, it can cause lag in acceleration. This is because a sufficient amount of fuel is needed for your engine to combust it optimally. Overall, this slow combustion can make your engine less powerful.
Bottom Line
The condition of your fuel system and diesel tank can significantly impact the performance of the engine. A routine offshore cleaning can ensure that all the components of the fuel system are clean and free from anything that can cause blockage, finally saving you from unexpected situations. For any assistance with offshore fuel tank cleaning and diesel filtration systems, feel free to contact us at Dit e-mailadres wordt beveiligd tegen spambots. JavaScript dient ingeschakeld te zijn om het te bekijken..How to Use Fuel Conditioner to Prevent Microbial Growth in Tanks
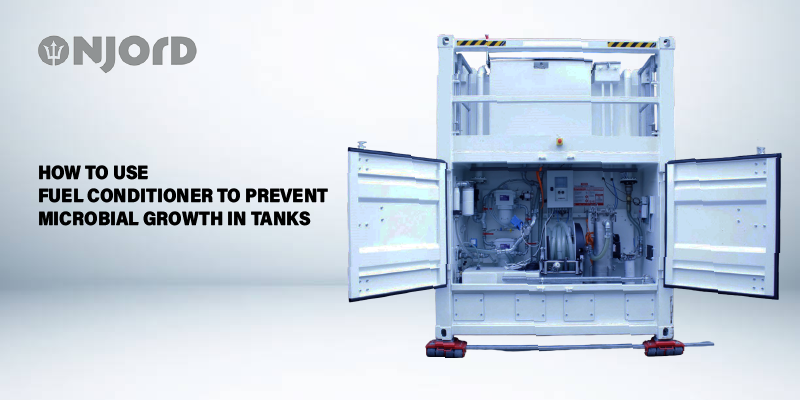
You must have seen how dark and cool the fuel tanks and storage systems can be. This is the perfect condition for aerobic and anaerobic bacteria or microbes to set in. So, if you have been avoiding your routine fuel system conditioning or cleaning, then it can lead to the development of dirty slime in your fuel system. This can further cause blockage in the filters and strainers in your fuel tank or storage, and can also be the cause of corrosion and spoilage. In this blog, we are going to discuss microbial growth in fuel systems and how you can use a fuel conditioner to prevent that microbial growth in tanks or storage.
What is Microbial Growth in Fuel Tanks?
Microbial growth in fuel tanks and storage is caused by bacteria and fungi that find the environment appropriate. If your tank or fuel temperature is between 10 and 40 degrees Celsius, then it can be a perfect atmosphere for microbes.
These microbes can easily be found in the ground or mud, and they enter your fuel tank while you fill or through vents during storage. Once contaminated, it can grow due to various reasons, such as water condensation at the base of the tank.
What Can You Do To Prevent Microbial Growth in Fuel Tanks?
Fuel Storage and Handling
Proper fuel storage and handling practices are needed to prevent microbial contamination. You can start by storing fuel in sanitary and dry tanks that have good ventilation. This will avoid exposure to air and moisture, which is the main cause of microbial growth. Furthermore, you can also use dedicated equipment to transfer fuel and reduce fuel agitation while storing or transporting.
Inspection and Maintenance
Remember to have regular checks and servicing of fuel tanks and storage so that you can take care of any issues in advance. Inspecting the tanks will help you find any signs of leakage or corrosion. You can also fix any damage before it affects your fuel quality. Finally, having clean tanks will help you keep an eye on fuel levels and temperature, which can minimize the chances of microbial growth.
Fuel Conditioners
You can use fuel conditioners , which are basically biocides. These chemical additives can kill the growth and activity of any microbes. Fuel conditioners can help you prevent microbial growth in tanks by disrupting their cell membranes or affecting their metabolic process. So, you can add fuel conditioners to your fuel tanks or storage to control and reduce the risk of not only fuel degradation but also equipment damage.
Fuel Stabilizers
You can use additives to improve the stability and shelf life of fuel in your storage tanks. They work by preventing oxidation and degradation that may promote microbial growth. Overall, they help prevent sludge and sediment formation so that only clean fuel goes into the fuel injectors. Further, you can also use fuel stabilizers to improve the fuel efficiency and prevent any water from getting into your fuel system.
Filtration
You need to use an advanced filtration system to remove all the particulate matter from your fuel tank and storage. The impurities in fuel can lead to microbial growth and ruin the quality. So, with a filtration system in place, you can reduce the risk of microbial contamination while improving the reliability of your fuel.
(Also Read: Fuel System Maintenance: Best Practices for Maintaining Reliable Fuel Quality )
Bottom Line
Implementing just a few steps can prevent microbial contamination in your fuel storage and tanks. If nothing else, you can simply use a fuel conditioner to prevent microbial growth in tanks. They not only improve the longevity of your engine and give you mileage, but also reduce emissions. You will find them also reasonably easy to use and priced easy on the pocket. For any queries related to preventing microbial growth or fuel conditioner, feel free to reach out to us at +31 (0)13 7640706.The Importance of a Water Separator in Diesel Fuel Polishing: Expert Advice
As you may already know, diesel is the heartbeat of every power system, especially in more significant industries like offshore marines, oil industries, etc. These big industries cannot compromise with either contaminated diesel or loss of power, considering this can lead to great damage and loss to the industry financially. This is why, in every big and small industry, one will always find a portable diesel fuel polisher for generators. These polishers ensure the fuel is dust and debris-free and enhance its overall quality for better and faster results.
But did you know that the water separator is the most essential part of a fuel polisher? It is no secret that despite oil and water not mixing well, water can, in offshore or extremely humid regions, mostly get inside the polisher and damage the overall quality of the fuel.
In today’s blog, we will discuss the importance of a water separator and the difference it can make. Keep reading about it with Njord Filtration.
But first…
What is a Water Separator in a Diesel Fuel Polisher?
Water can quickly degrade the quality of diesel fuel due to many underlying reasons, including humidity, poor fuel storage, condensation, etc. This will not only damage the fuel's potential but also cause serious engine problems, resulting in frequent blackouts in the industry. A water separator, in this case, ensures that the water is removed from the fuel, enhancing its overall quality.
Let us explain how a water separator can help the industrial diesel fuel polisher machine work more effectively. So, technically, a water separator ensures that:
- It sits nicely in the fuel polishing machine, and as the fuel flows, the separator detects and traps the water.
- During this process, the water settles at the bottom while the fuel continues to undergo the next stage of filtration.
- Once the water is successfully separated, the drain valve attached to the separator automatically drains it.
(Also read from our previous blogs: Choosing the Right Diesel Filtration System for Oil Industry Needs with Njord Filtration)
The importance of the Water Separator
As you already know, water and fuel do not mix well. If you do not clean the fuel and keep it free from moisture and water, it can result in system damage, frequent breakdowns, engine failures, or microbial growth that can cause permanent damage to the machinery.
The reason why the water separator plays an important role here is that:
- Water separators prevent microbial growth, ensuring there is no growing space for fuel-eating microbes.
- When the fuel is 100% water-free, it burns more efficiently, resulting in improved power output.
- Water-separating units ensure the fuel is clean and dry, which in turn prevents rust in the pumps, injectors, and filters.
- One of the most important factors is that water separators ensure the fuel quality is up to the mark so that emergency breakdowns can be avoided, especially in boats, yachts, etc.
Key benefits of using a Water Separator
When industries go for a diesel fuel polisher with water separator, they get direct benefits like:
- Eliminating water before it reaches the engine.
- Increases the lifeline of the fuel.
- Reduces the overall maintenance costs.
- Prevents the growth of microorganisms.
- Improves fuel efficiency.
Why Choose the Njord Diesel Polishing System with Water Separator?
In simple terms, when you choose Njord Filtration, you get:
- Automatic fuel polisher for storage tanks
- A compact and modular design
- Advanced multi-stage filtration
- Trusted brand and after-sales consultancy
Bottom Line
Big industry or small, you must always invest in Njord Filtration’s reliable and portable diesel fuel polisher for generators. This all-in-one component ensures the quality of the fuel for seamless industry backups.
Talk to a Njord specialist about how to protect your diesel system—schedule a 15-minute consultation today.”Contact us here.